Stainless steel corrosion-resistance and anti-coking technology
A WORLD'S LEADING SURFACE ENHANCEMENT TECHNOLOGY
CTS is a surface enhancement technology by in situ surface modifications of stainless steel through chemical-electrochemical methods. It improves the corrosion resistance and anti-coking performance of stainless steel greatly.
CTS technology is developed to solve the widespread problems of equipment corrosion and coking in the industrial environments. It is for industries with complex corrosive media and wide temperature and pressure ranges such as in petrochemical, coal chemical, marine, electric power, and metallurgy industries. It allows more selections compared with traditional materials. CTS technology can effectively slows down the corrosion of equipment by chlorine, sulfur (sulfide), and organic acid (naphthenic acid). It is also characterized by anti-coking and anti-scaling, etc., thereby meeting the needs of industrial equipments in terms of safety, cost reduction, and efficiency improvement.
Corrosion resistance Anti-coking Improved wettability Strong adhesion Wide temperature range Without affecting the mechanical properties of the raw material Without affecting the heat transfer performance of the raw material |
![]() |
Pitting resistance index of film (PREN):≥40
Film thickness:≥100nm
Film adhesion: Thermal shock test (450 ℃): the film shall not bubble or fall off
FeCl3 corrosion test: The corrosion rate is less than 1/3 of the base material
Film appearance: The primary color of stainless steel disappears and it appears in color.
After years of industrial testing and application, it has been proved that the technology is safe, reliable, stable and excellent in performance.
The chromium oxide content in the film is as high as more than 70% (wt), and the pitting resistance index (PREN) reaches 40 ~ 58.
The service life of the equipment can be prolonged to 2 ~ 5 production cycles
The capacity of the surface of the material to absorb ions is greatly reduced, which can effectively alleviate the tendency of scaling and coking in the system.
It can improve the service life of equipment by 200%-500% and reduce the initial cost and the replacement cost of equipment.
It can maintain the continuous stability of the mass transfer and heat transfer performances of material surface, avoid the efficiency reduction of equipment in long-term operation, ensure a long-term, safe, and stable operation of equipment, and reduce the operating costs.
A stable processing performance makes equipment maintenance and prediction more accurate, and avoids losses caused by accidents.
The safe operation index of the whole system is improved, the metal ions with adverse effects in the system are greatly reduced, and other subsystems, such as catalysts, are protected for longterm.
It reduces the discharge of solid wastes and hazardous wastes, and the use of chemical cleaning agents, that makes it safer and more friendly to the environment.
CTS technology is widely used in:
Petrochemical, coal chemical, marine engineering, electric power, metallurgy and other industrial fields;
410S/304/304L/321/316/316L/317/317L/904L/2205/2507/N03867 ferritic stainless steel, austenitic stainless steel, duplex steel and super stainless steel;
Internals, heat exchangers, pipes, containers, moving equipments (pump impellers), etc.
According to customer needs, we can provide CTS technology surface treatment services for customers;
We can also provide customers with CTS-treated internals and equipments.
Transportable parts and equipment can be delivered to Candor’s plant for treatment;
Large-sized equipment (containers, etc.) , that cannot be moved, can be treated at customers’ site.
A liquid distributor is the core component of the packed tower, which is of great significance to improving the separation efficiency, ensuring product quality, and increasing the product yield. As a patented product of Candor (Patent No.: ZL99248216.X), compared with the traditional narrow trough liquid distributor, the three-stage baffle narrow trough liquid distributor can improve distribution efficiency by 10% ~ 50%, and a very uniform and continuous liquid film formed at the bottom edge of the guide plate, especially in case of low liquid volume. It is also capable of generating uniform droplets parallel to the trough and at the bottom edge of the guide plate. The lower the liquid head is, the greater the efficiency is improved. This structure allows effective coordination and selection on hole number, hole diameter, and hole spacing on the trough, in order to meet the requirements of uniform liquid distribution and design elasticity. In case of very low liquid volumes, the three-stage guide plate is also provided with concave pits arranged according to a certain rule, which can eliminate the uneven distribution caused by the contraction of liquid on the metal surface and partially eliminate the unevenness caused by the levelness error when the distributor is installed in industry.
Highlights of three-stage guide plate trough liquid distributor:
1. Good distribution performance.
2. High elasticity of operating loads.
3. Good cushioning performance.
In 2001, the patented technology of three-stage guide plate liquid distributor of Candor was successfully applied to the vacuum tower of a 8 million tons/year atmospheric and vacuum distillation plant in the refinery of Sinopec Shanghai Gaoqiao Branch, which had the largest tower diameter (10.2 m) in that year in China. The team won the Sinopec Science and Technology Progress Award in May 2005 because of the excellent performace of the unit.
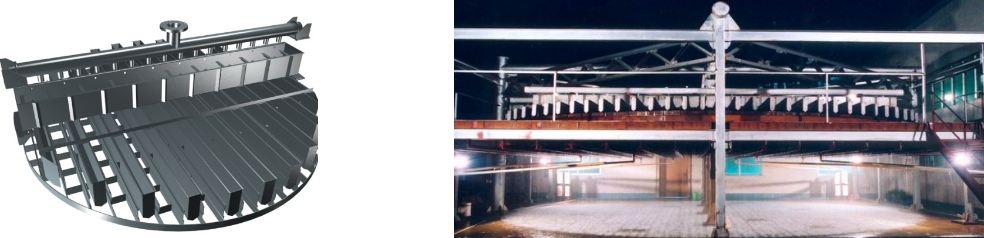
In order to solve the contradiction between liquid collection and gas distribution in a oil tank,and also the problem that the heated structure is easyly to deformed or even destroyed in high-temperature, Candor has developed a patented technology (Patent No.: ZL 2010 2 0662927. 9) - the beam-trough integrated oil collecting tank. It greatly reduces the overall height of the oil collecting tank, improves the liquid storage capacity, increases the area of the gas phase channels, reduces the use of materials and is more cost-effective by replacing the support beam with the liquid collection structure and the trough. |
Due to the high temperature and low spray density in the washing section of a vacuum tower, the oil collecting tank might be seriously coked, and the structure of a oil collecting tank is easily damaged due to high temperature. Through the integrated structure of two or more trough beams arranged in the middle, a plurality of liquid collecting troughs are arranged between the two or more trough beams to guide liquid into the larger trough, and by ensuring a certain inclination, the flow path of the liquid is shortened, the retention time of the collected liquid is reduced, and coking is prevented. In addition, the common truss beam is replaced by the trough, and the material cost is reduced. The liquid collecting trough is connected slidabley with the tower wall support, and can freely expand at high temperature, therefore it is not limited by the operating temperature and is convenient to disassemble. Through the optimized arrangement, the vent area is much larger than that of the conventional oil collecting tank, which is especially suitable for occasions where the pressure drop of the internals is strictly limited by in a deep distillation of the vacuum tower. |
V-blade feed distributor High-speed gas quickly passes through the middle channel of the distributor and then passes through the channels formed by the arc-shaped fins which are optimizedly arranged to disperse the gas, thereby achieving the purpose of converting kinetic energy, simultaneously enabling the gas to be distributed with high uniformity. The design improves the separation efficiency of the tower. Highlights: (1)Uniform distribution of feeding gas phase. (2) Less scouring of the tower wall. (3)Lower resistance. (4)Simple structure, convenient in installation and replacement, and small occupied space. Double-tangential circumfluence type feed distributor The feed distributor has a separation function of one theoretical plate, which is suitable for vapor-liquid two-phase feed, and is generally used for the feed inlet at the bottom of a tower. The non-uniformity is less than 0.37%, the liquid entrainment in the vapor stream is less than 0.1%, and the pressure drop is less than 0.7 mmHg, therefore it has the best comprehensive performance. Hightlights: (1)lower pressure drop, and less energy consumption; (2)lower entrainment rate and the distribution of gas and liquid phases is more uniform; (3)better separation effects. |
Without changing the original specific surface area and the main body inclination angle of the plate corrugated packing, the inclination angle of the joint part of the upper and lower layers of packing is improved, so that the original 90° sharp corner is changed into a gentle corner, which effectively reduces the resistance drop of the packing and improves the processing capacity (reduces the flooding rate), which is unique in dealing with coking easily and easily polymerized materials. Highlights: (1)Low pressure drop (2)High efficiency (3)Large processing capacity |
Type | Name | Models and specifications |
Trough liquid (re) distributor | Three-stage guide plate narrow trough liquid distributor | CFY11 series |
Three-stage guide plate narrow trough liquid redistributor | CFY12 series | |
Primary trough liquid distributor | CFY13 series | |
Primary trough liquid redistributor | CFY14 series | |
Tubular liquid distributor | Tubular liquid distributor | CFY21 series |
Tray liquid distributor | Drip tray liquid distributor | CFY31 series |
Drip tray liquid redistributor | CFY32 series | |
Duplex trough tray liquid distributor | CFY33 series | |
Duplex trough tray liquid redistributor | CFY34 series | |
Liquid-liquid extraction distributor | Coil extraction distributor | CFC11 series |
Calandria extraction distributor | CFC12 series | |
Sieve plate extraction redistributor | CFC21 series | |
Gas distributor | Guide plate gas distributor | CFQ11 series |
Riser gas distributor | CFQ21 series | |
Feeder | Tray flash feeder | CJL10 series |
Perforated straight tube feeder | CJL20 series | |
Straight pipe baffle feeder | CJL30 series | |
Single tangential loop feeder | CJL40 series | |
Double tangential loop feeder | CJL50 series | |
V-blade feeder | CJL60 series | |
Calandria feeder | CJL70 series | |
Liquid collector | W-type liquid collector | CSY10 series |
V-type liquid collector | CSY20 series | |
Improved oil collecting tank | CSY30 series | |
KRJ-type oil collecting tank | CSY40 series | |
Beam-trough integrated oil collecting tank | CSY50 series | |
Packing support | Support grille | CZC10 series |
Hump-type support plate | CZC20 series | |
Mist catcher | Mesh-type mist catcher | CQT21 series |
Folded plate mist catcher | CQT22 series | |
Demister | Herringbone demister | CQT31 series |
Fiber type demister | CQT32 series | |
Tray | Combined directed float valve tray | |
Fixed tongue tray | CBF12 | |
F1 float valve tray /span> | CBF13 | |
Bubble cap tray | CBF14 | |
Multi-downcomer MD tray | CBF15 | |
Structured packing | Metal wire mesh corrugated packing | |
Metal orifice plate corrugated packing | ||
Candor new packing | ||
Plastic wire mesh corrugated packing | ||
Plastic orifice plate corrugated packing | ||
Bulk packing | QH-1 type flat ring | |
QH-3 type flat ring | ||
Intalox saddle ring | ||
Pall ring |
Process design and optimization
Development of energy-saving and efficiency-increasing long-period technologyEquipment design and selection
On-site services